
If you try to find the causes of a problem too quickly, you’ll be in danger of discovering only some of the causes but overlooking the most important ones. If a cause is overlooked, the whole project might be in peril.
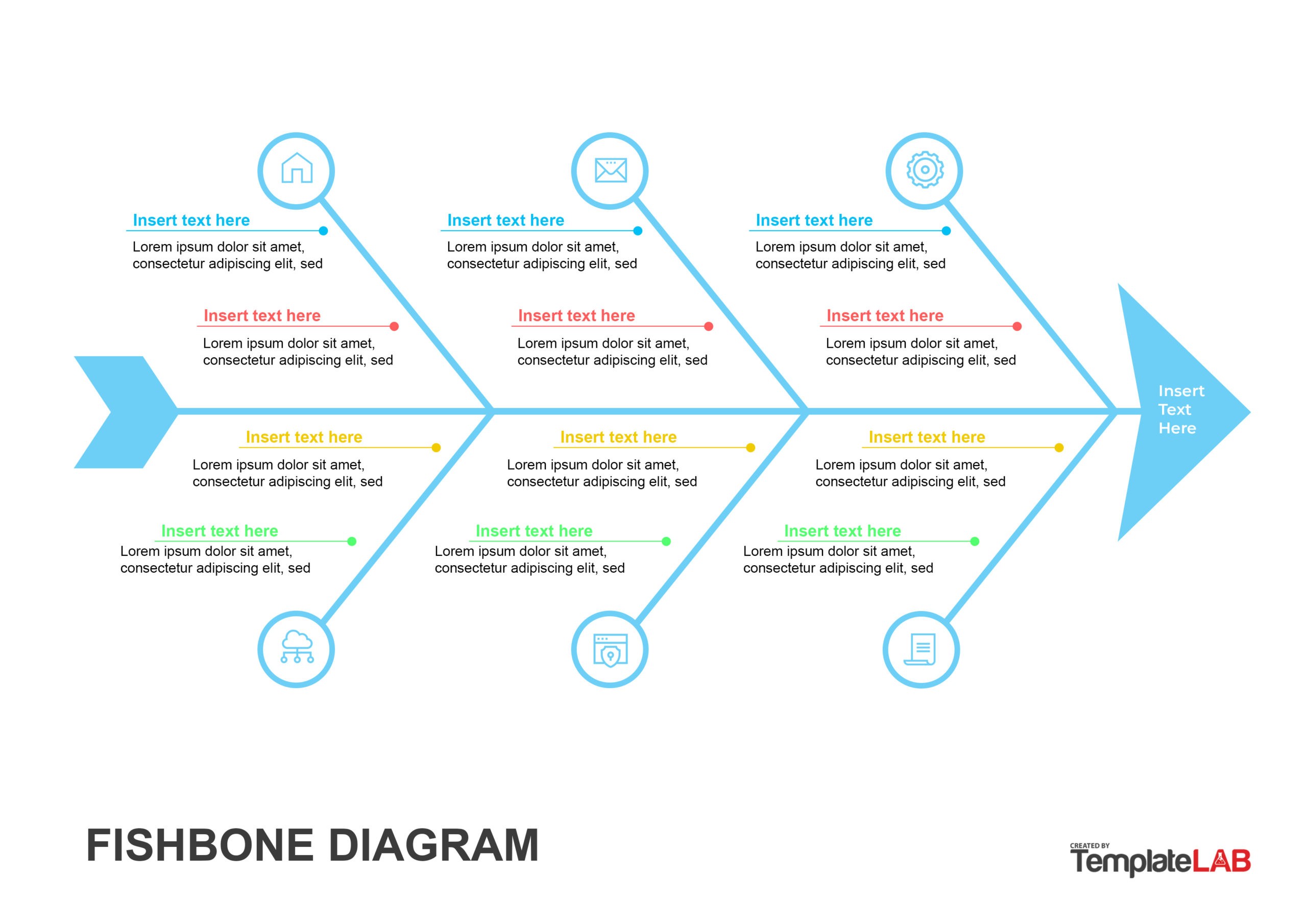
Rushing the process is counter-productive. Here the “why” question is asked five times in order to get to the root of the problem.Ī solution to the problem requires time. In order to find the real cause of a problem, the 5W method is used. For example, the rudeness of the customers could be explained by excessively long waiting times on the hotline. The defect, or the problem to be solved, is shown as the fishs head, facing to the right, with the causes extending to the left as fishbones the ribs branch. With such a level of detail, the causes of the problem can then be determined. When analyzing the problem, further subcategories can be elaborated upon. Also “Lack of knowledge on the customer’s part” as well as “Rudeness of the customer” could be added. As a group all potential causes are to be identified.įor example, under “Material” it would be a good idea to comment on the type of customer inquiry. Brainstorming is required in order to find the causes. The team should be mixed since if people with different expertise are involved, there’s more chance it will lead to extraordinary ideas. In particular, it should be done with those employees, who are directly involved in the problem-causing processes. It is recommended to complete the fishbone diagram as a team. Next to the category lines, the specific causes of the problem can be added. Step 3: Drag the rectangular Category 1 or Category 2. In the second step, from the cause and effect diagram, drag and drop the fishbone shape onto the left side at the canvas. Step 2: Drag fish shape within the diagram. When using the 8M method, three additional factors are used: The easiest way is to create a fishbone diagram by picking a fishbone diagram and edit it or choose a template and edit. The 5M method also uses the additional factor of: The 4M method uses the following main influencing factors: They refer to the main influencing factors of processes, which often lead to problems. When specifying the potential causes of the problem, you can use several methods: the 4M method, and its extensions the 5M and 8M methods, are frequently used.
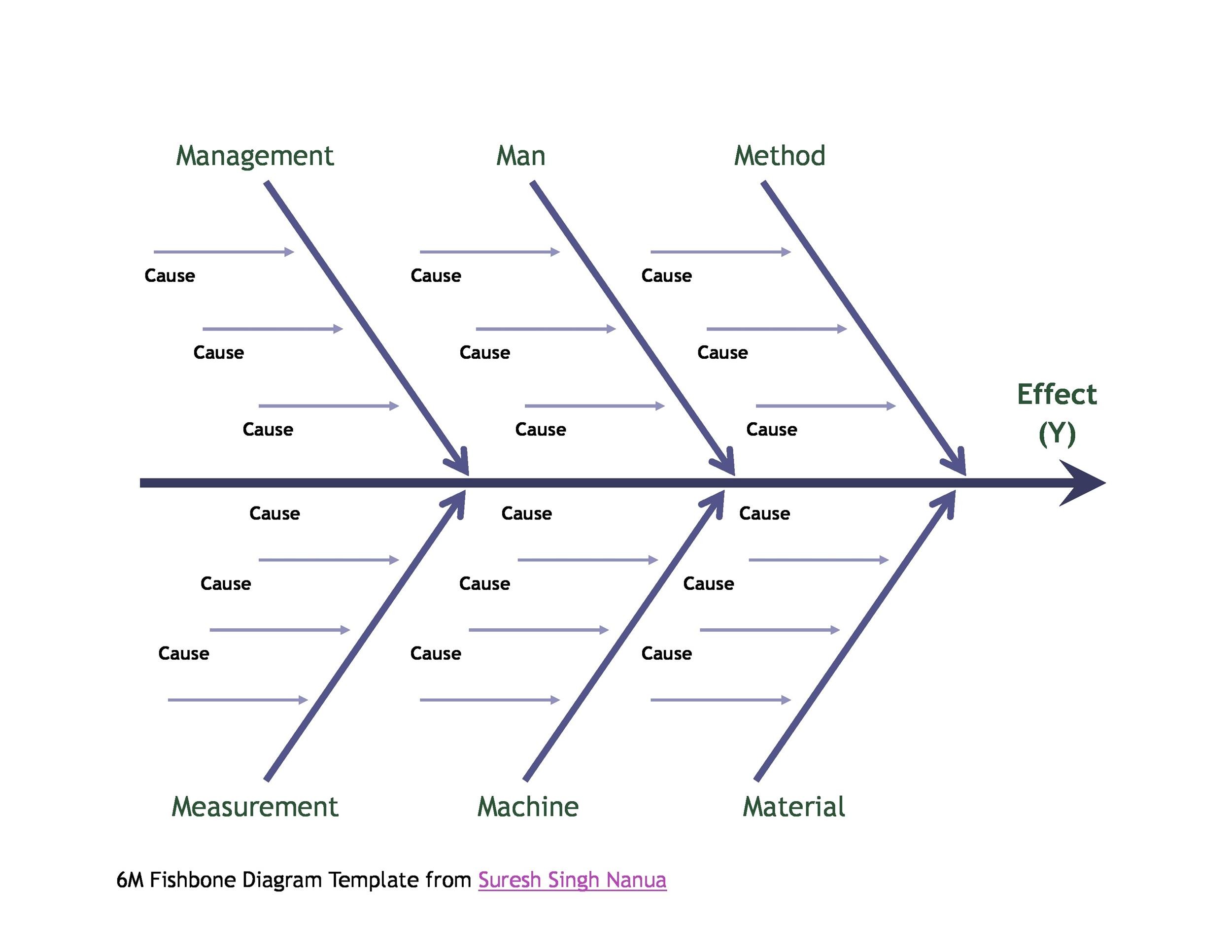
Several other lines branch off from this main line: the possible causes of the problem. You then draw a line or an arrow to the left i.e. Be as accurate as possible when describing the problem and write it on the right hand side of the flip chart or blackboard. It is written down before any other observations are made. The problem that needs to be addressed is on the right side of the diagram. Every problem, requiring a sustainable solution, is graphically illustrated with its respective causes in the diagram. It is therefore also called the cause-effect diagram. The fishbone diagram, invented by Ishikawa Kaoru, a Japanese chemist, (hence why it is also referred to as the Ishikawa diagram) aims to help companies find solutions to problems and their causes in a structured way.
